What is Formwork or Shuttering:-
Concrete, in which concrete is poured and cast in the desired shape and gain initial strength, hardened and matured. Formwork is used in different shapes and sizes according to our construction elements in the form of PCC, RCC works in Building, Bridge, Tunnel Lining, Hydropower Dam, Irrigation Headwork, Sanitary Pipeline work, etc.
The cost of formwork is considered as 20 to 25% of the cost of the structure in building work, it may be higher than this in bridges. In order to reduce the cost of form, it is necessary to design economical types of formwork and to mechanize its construction.
We should have to remove the form work when concrete has reached a suitable strength. That process of removal of formwork is also called stripping. After stripping of form it’s components are removed and can be used in other construction processes or other parts of work. The repeatable type of formwork components is known as a panel form.
Formworks on the basis of Materials:
On the basis of materials, Forms are followings types:
- Wooden form,
- Plywood form,
- Steel form,
- Combined wood-steel form,
- Reinforced concrete form, and
- Plain concrete form.
Above this, timber is normally used as formwork and it is also cheap. But there is the possibility of warping, swelling, and shrinkage of the timber is a drawback of timber.
We can reduce these defects by application of the water-impermeable coatings on the shuttering. This impermeable coating also helps to stripping and, also prevent from adhering to the concrete.
Steel shuttering is used for proper shape and function with asthetics to be achieve.
Advantages of steel formwork is given below:
- It can be used for many numbers of times,
- Stripping process is easy in steel formwork,
- A uniform charming and smooth surface finish by using steel formwork,
- The rigidity is high in steel formwork,
- Shrinkage or distortion is less in concrete by using it.
- The edge and other special shapes in the structure can be easily cast by steel formwork.
Materials used in concrete Shuttering:
1. Steel formwork
Using steel in formwork increases the initial cost, but in the long run, it proves to be economical as it can be re-used more times, normally ten times more than timber formwork. The further finishing treatment is less after using steel shuttering because it gives excellent exposed concrete surfaces.
As steel has no ability to absorb water concrete and hence, there are negligible chances of formation of the honey-combed surface. It is easy to dismantle and possesses more strength and durability compared to others.
2. Conventional timber formwork
It is generally used for small works requiring fewer repetitions since its initial cost is less. It is better to use timber with free from loose knots, light in weight and easily, workable with nails without splitting and should be well-seasoned. These formworks can be re-used for 10 to 12 times.
3. Plywood formwork
Using plywood in formwork is gaining popularity given that it presents a smooth surface that requires no further finishing treatment and can also be re-used normally 20 to 25 times. Plywood can be used to cover up the large area so that it largely reduces the labor cost of fixing and dismantling of formwork.
Requirement for Good formwork (Shuttering)
A good formwork should satisfy the followings requirements:
- The material of the formwork should be cheap and it should be suitable for reuse several times.
- The form should be practically waterproof so that it does not leak and absorb water from concrete. Also, its shrinkage and swelling should be minimal.
- It should easily carry the load of concrete and live load of pouring, vibration, compaction, and curing.
- It should have enough stiffness and rigidity so that deflection is minimum.
- As soon as possible it should be light in weight, smooth and should be easily stoppable.
- All the joints in formwork should be leakproof.
- The formwork should rest on non-movable supports.
CODE PROVISION FOR STANDARD FORMWORKS (SHUTTERING)
- General requirement:
The formwork shall conform to the orientation, lines, and dimensions, as shown the plans and be so constructed on remain sufficiently rigid during the placing and compacting of the concrete, and shall be sufficiently tight to stop loss of liquid from the concrete.
2. Cleaning and treatment of forms:
All rubbish, particularly chippings, shavings, and sawdust, shall be faraway from the inside of the forms before the concrete is placed and therefore the formwork in touch with the concrete shall be cleaned and thoroughly wetted or reacted with an approved composition. Keep in mind that that approved composition should be kept not be touching the reinforcement.
3. Stripping time:
In no circumstances, forms shall be struck until the concrete reaches a strength of a minimum of twice the strain to which the concrete could even be subjected at the time of striking.
As soon as possible for a longer time, the formwork should be kept in contact, because it might withstand the curing. In normal condition, generally when the temperature is above 20 ⁰C and where ordinary cement is used, forms can be stripped after the following periods:
- For Walls, columns and vertical sides of beams – 24 to 48 hours as may be according to side condition recommended by engineer-in-charge.
- In Slab soffits (props left under) – 3 days.
- In Beam soffits (props left under) – 7 days.
- Removal of props to slabs: For slab Spanning up to 4.5 m – 7 Days For slab Spanning over 4.5 m – 14 Days
- In the beams and arches props can be removed as :
- For member Spanning up to 6 m – 14 days.
- For member Spanning over 6 m – 21 days.
Note: Number of props, their sizes, and position, shall be such as to be able to safely carry the full load of the slabs, beam or arch as the case may be.
4. Procedure when removing the formwork:
At the time of removal of formwork keep in mind that there is no shock or vibration as that would damage the reinforced concrete. Before the soffit and struts are removed, the concrete surface shall be watched out, where necessary so as to determine that the concrete has sufficient strength and hardened. Proper precaution shall be taken to permit for the decrease within the rate of hardening that happens with all cement in, the cold water not be done unless allowed for in design calculations of the beams.
5. Camber:
It is generally desirable to offer forms an upward camber to make sure that the beams don’t have a sag once they have kept up their deflection, but this could not be done unless recommended by the calculated design of the beams.
6. Tolerances:
Formwork shall be so constructed that the interior dimensions are within the permissible tolerance specified by the designer.
Loads on Formwork (Shuttering)
Apart from its own load following loads occur on formwork:
- Live load due to labor etc.
- The deadweight of wet concrete,
- The hydrostatic pressure of the fluid concrete acting against the vertical or inclined faces of form, and
- Impact due to pouring concrete.
- Vibrational Load due to vibrator during work.
- Erection stresses due to movable equipment.
Shuttering (Formwork) for Concrete Column
Shuttering for a column is simple as compare to other complex structural elements.
Column Formwork consists of the following main components:
- Sheeting all around the column periphery,
- Side yokes and end yokes,
- wedges, and
- Bolts with washers.
Figure below is the detail of the formwork for a square column.
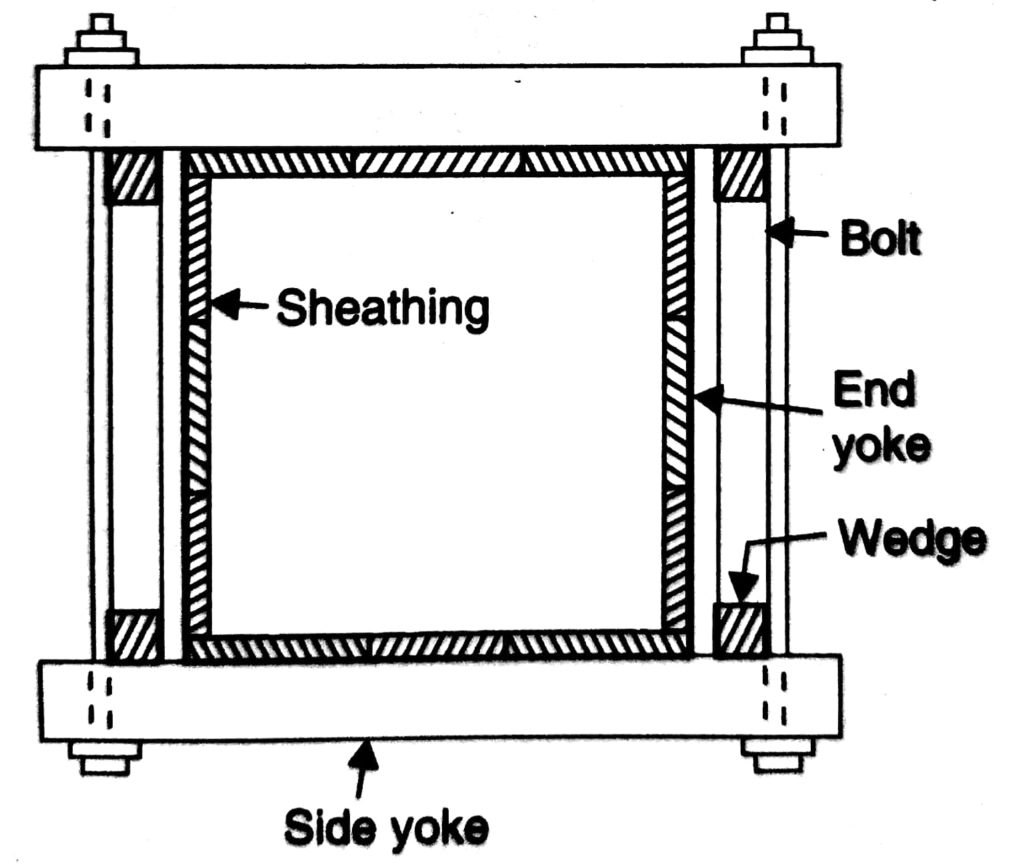
Fig. 1. Formwork for square or rectangular column.
In this formwork, the side yokes and end yokes contain two numbers each and are perfectly placed alongside the peak of the column. Generally, the two-side yokes are comparatively of the weighted section and are tagged together by two long bolts of 16 mm dia perfectly. Between the bolts and the end yokes, four wedges, one at each corner, are inserted. The sheathing is fixed by nail to the yokes.
Figure 2. below shows shutterings for octagonal and round columns.
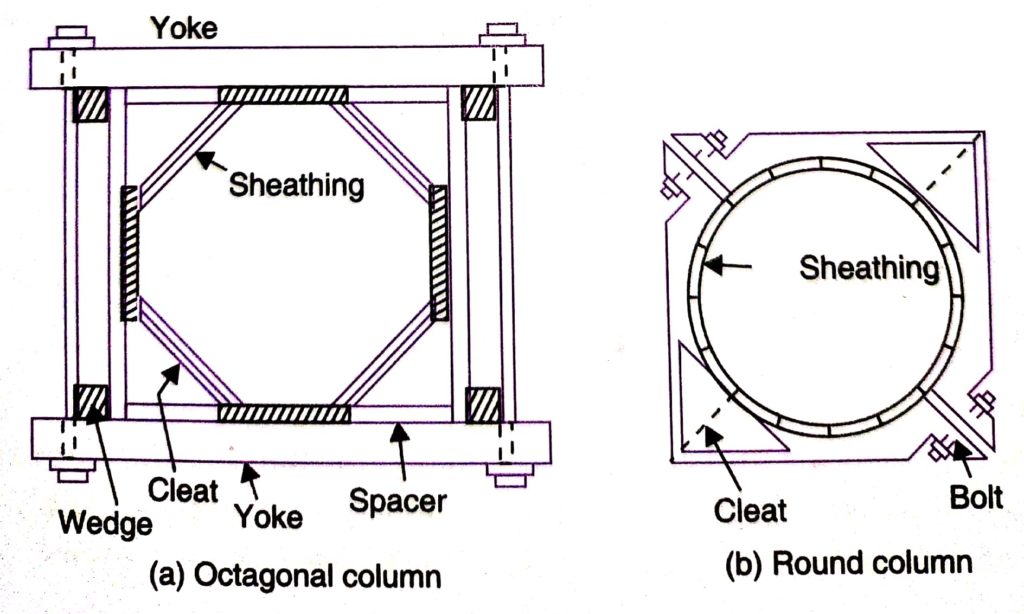
Fig.2. A Typical section of Octagonal and Round Column
Shuttering For Beam and Slab Floor
Figure .3. shows the formwork for the beam and slab floor. As shown in the fig the slab is continuous over a number of beams. The slab is supported on 2.5 cm thick sheathing laid parallel to the most beams. Normally, the sheathing is held on wooden battens which are laid between the beams, at some suitable spacing.
In order to scale back deflection, the battens could also be propped within the middle of the span through joists. In the side forms of the beam, 3 cm thick sheathing is used. The bottom sheathing of the beam form maybe 5 to 7 cm thick.
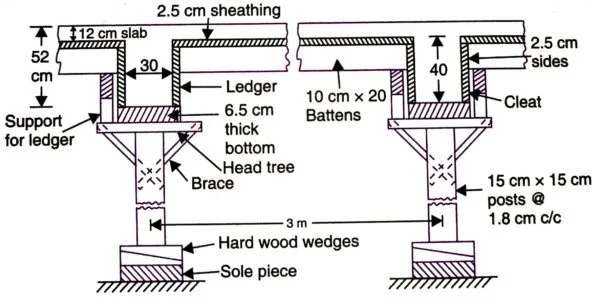
Fig. 4. shuttering for beam and Slab floor- section
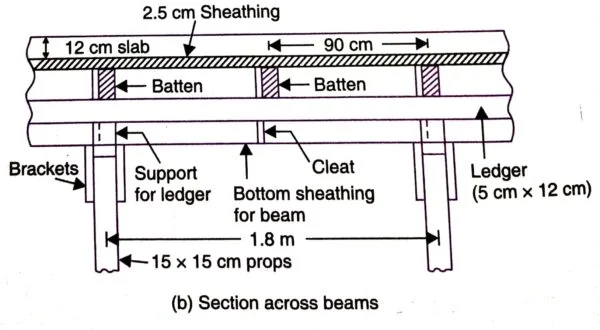
Fig. 5. Shuttering in Beams and slabs floor – section across beams
The ends of the battens are supported on the ledger which is fitted to the cleats throughout the length. Cleats 10 cm x 2 cm to three cmare fixed to the side forms at an equivalent spacing as that of battens, in order that battens could also be fixed to them. The shore or post is connected to the top tree through cleats. At the bottom of the share, two wedges of hardwood are provided over a sole piece.
Concrete Stairs Formwork (Shuttering )
As shown in fig.6. The following are the components used in concrete Stairs formwork: Cross joists, String, Stiffener, Risers, Decking, Ledger, Cut String, Hangers, Boards, Strut, etc.
The risers planks are 4 to 5 cm thick and equal to the height of the riser. These planks are beveled at the bottom to permit the whole of the tread faced to be trowelled.
The riser planks are placed after the reinforcement has been fixed in position. The treads are left open for placement of concreting and vibration. Normally as shown in the fig the stiffener is wired to cross-joists through the decking. You can see all the details in these diagrams 5. & 6. below :
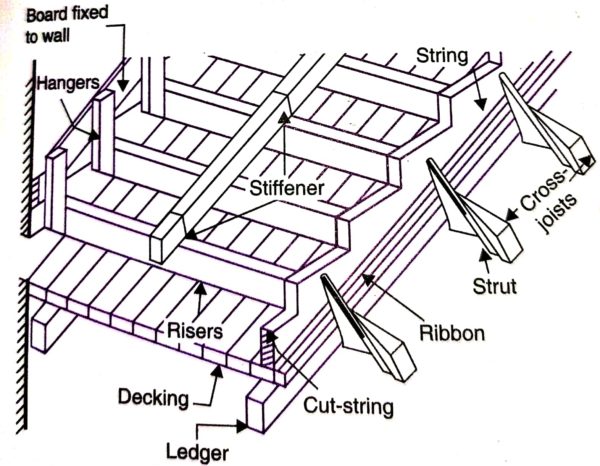
Fig. 6. Form work for Stairs – Top view
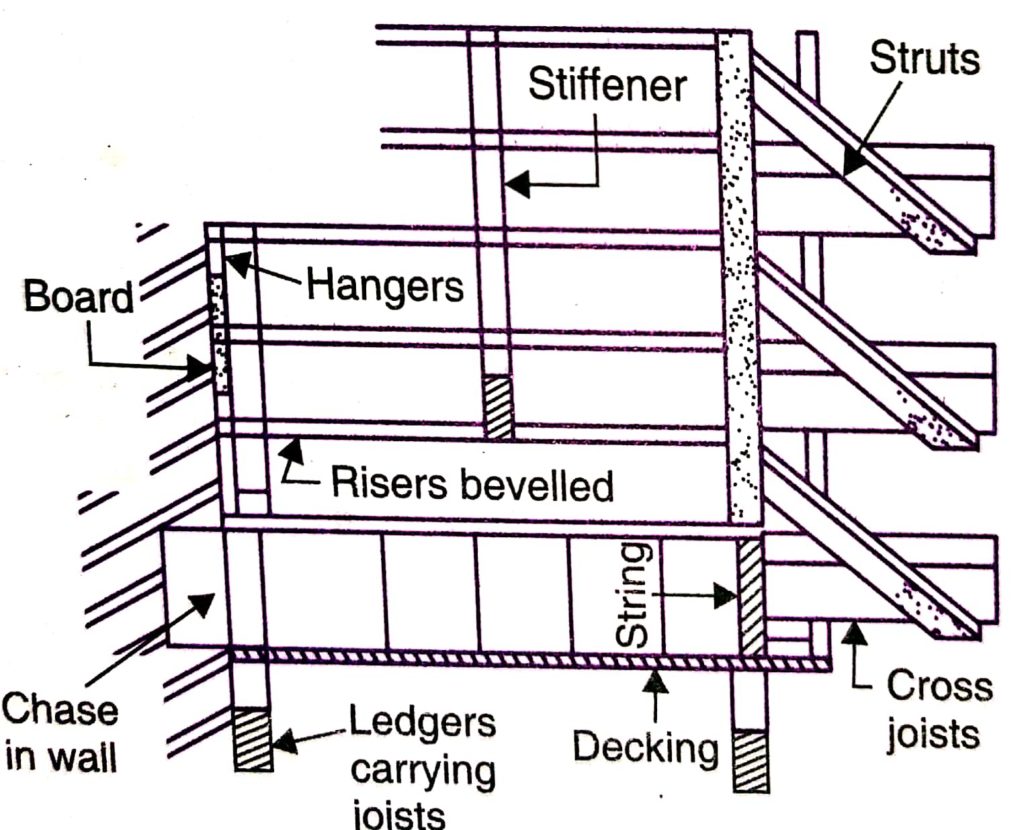
Fig. 6. Form work for Stairs – Cross section view
Formworks (Shuttering) for Walls
Figure 26.5 shows the fixed form for walls. In the Wall formwork following components are used: Stake, Wedge, Studs, Soleplate, Blocking pieces, Wellings, Twisted wire, Spacer, Concrete kicker, etc.
The boarding of a specified thickness is used. The boards are fixed to 5 cm x 10 cm posts, known as studs or soldiers, spaced at about 0.8 m apart. Horizontal whalings of size 7.5 cm x 10 cm are fixed to the posts at suitable intervals. After that, the whole assembly is strutted as shown in the fig, using 7.5 cm 10 cm struts.
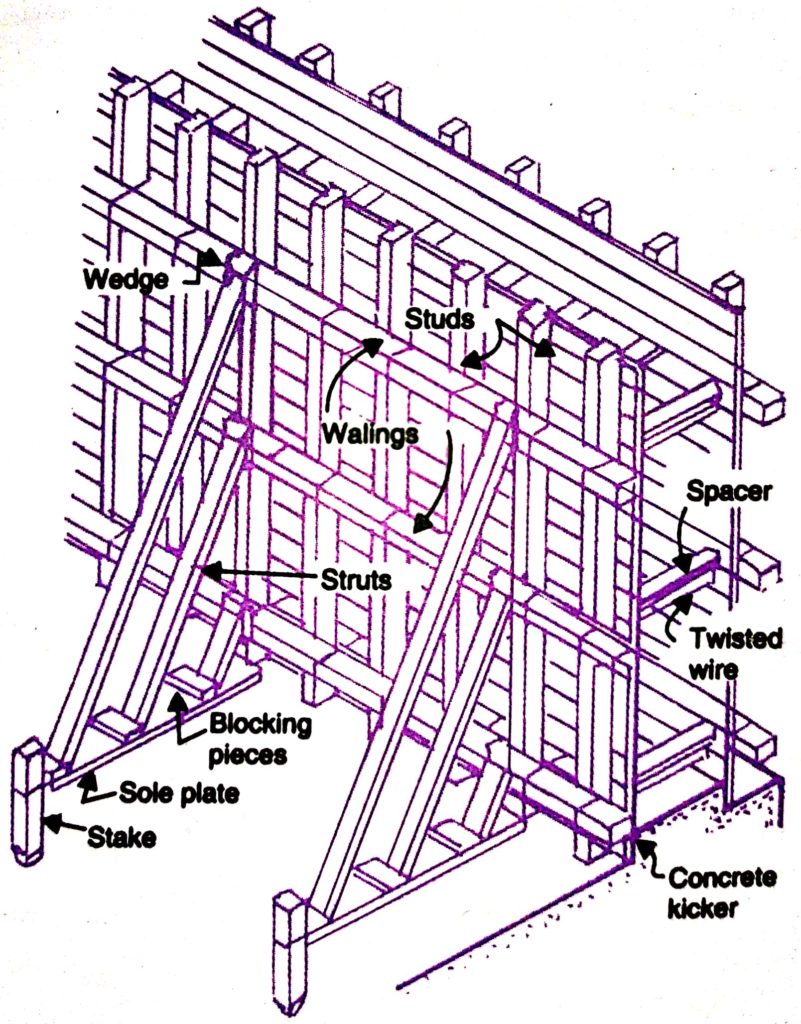
Fig. 7. Formwork for Wall – Fixed type
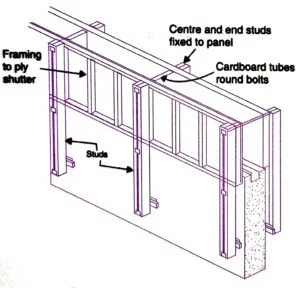
Fig. 8. Formwork for wall – Moving wall type
The two shutters are kept apart equal to the thickness of the wall, by providing a 5 cm high concrete kicker at the bottom and by 2.5 cm x 5 cm spacers nailed to the posts.
Figure 26.6 shows moving form for the wall. In these, the forms are made up in a panel size of 0.6 m x 1.8 m so that handling and stripping are easier.
Generally, boarding is not used only 15 mm plywood is used. The panels are erected in such how that the lower panels are often removed when concrete is tough and used above the wall.
Framing of size 5 cm x 10 cm is used to the Ply shutter. It is very important to fix the panels central and two ends are studs. Each stud consists of two Pieces of timbers, 5 cm x 15 cm, blocked apart.
The end strut of each panel secures the adjacent Panel. Boards are reversed for Ist lift; for succeeding lifts, bolts pass through holes formed to Previous lift.
For the rapid construction of a constant thickness wall, continuously rising form, commonly known as a sliding shutter is used. The shutter may rise at the rate of 15 to 30 cm per hour depending upon the rate of hardening of concrete. Either a hydraulic Jack or a manually operated screw jack may be used for raising the form.